Das goldene Zeitalter der industriellen Dienstleistungen?
Lithium-Ionen-Batterie, Brennstoffzelle oder Biogas – welches ist die Antriebstechnologie der Zukunft?
Dr. Christoph Jaschinski: Batterien, vor allem optimierte Lithium-Ionen-Batterien, werden heute weltweit als eine Schlüsseltechnologie für die Antriebe der Zukunft gesehen. Viele Hersteller und Zulieferer experimentieren zwar auch mit anderen Kraftstoffen und Antriebstechnologien wie Wasserstoff in Kombination mit der Brennstoffzelle oder synthetischen Kraftstoffen. Doch es zeigt sich, dass zumindest mittelfristig für Pkw der Fokus auf Fahrzeugen mit Lithium-Ionen-Batterien liegen wird. So wird bis 2030 erwartet, dass allein in Deutschland mehr als 4,5 Millionen elektrische Fahrzeuge jährlich produziert werden. Jüngste Schätzungen gehen davon aus, dass in Europa bereits dieses Jahr über 4,6 Millionen Fahrzeuge mit Batterieantrieb verkauft werden. Diese wachsende Nachfrage stellt die Industrie weiter vor große Herausforderungen. Das beginnt bei der Planung und dem Hochlauf neuer Werke, geht über die Transformation bestehender Werke zu effizienten und kostengünstigen Betreiberkonzepten und endet bei der Supply Chain. Hier sind spezialisierte, technische Dienstleister gefragt – mit Fachwissen rund um die moderne Fabrikorganisation.
Was muss ein derartiger Dienstleister mitbringen?
Die Anforderungen unterscheiden sich je nach Stufe der Wertschöpfung. Bei der Fahrzeugmontage, also der Hochzeit des Batteriespeichers mit der Karosserie, geht es vor allem um Know-how in der Realisierung oder um Planungs- und Betreiberkompetenz für die komplette Intralogistik der Hochvoltspeicher. Anders sieht es bei den Montagewerken für die Batteriepacks aus. Hier braucht es spezielle Planungskompetenzen in der Montagetechnik, der Automatisierung und der Analysetechnik, aber auch in der Qualitätssicherung und -kontrolle. Besonders anspruchsvoll ist die eigentliche Fertigung der Batteriezellen. Hier fehlt es in Europa an Prozesswissen, außerdem ändern sich die Fertigungstechnologien noch sehr rasch. Die Industrie fordert zum Beispiel Kenntnisse rund um Smart Factory Analytics, agiles Arbeiten oder Anlagentechniken, die oft nur gemeinsam mit Anlagenbauern entwickelt werden können.
Welche Erfahrungen kann Leadec vorweisen?
Wir haben Referenzen für Teststellungen und in der Großserienfertigung durch Projekte in Deutschland, Polen und den USA. Dabei hat sich gezeigt, dass die Hersteller vor allem an technischen Dienstleistungen interessiert sind. Das Engineering, die Instandhaltung von neuen Montagelinien, Dienstleistungen für die Vormontage und die Versorgungslogistik stehen ganz oben. Ein Beispiel: Unter anderem arbeitet Leadec mit einem Tochterunternehmen der Daimler AG zusammen. In Kamenz bei Dresden werden hoch entwickelte Lithium-Ionen-Batterien für Plug-in-Hybride oder rein elektrische Fahrzeuge gebaut.
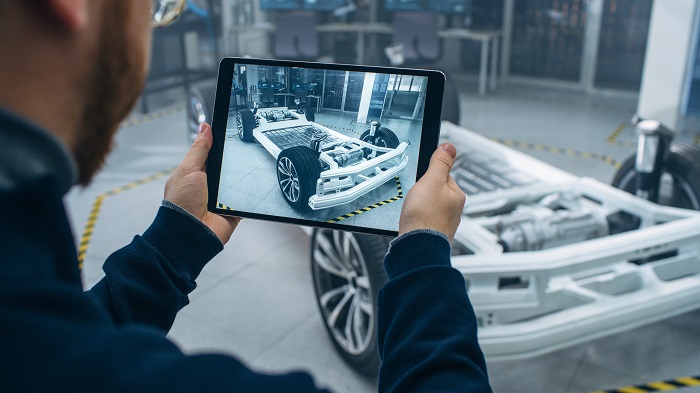
Leadec hat hier innerhalb weniger Monate an einem eigenen Standort außerhalb des Werksgeländes ein Betreiberkonzept zur Vormontage unterschiedlicher Batteriepackgehäuse geplant und umgesetzt. Das innovative Versorgungskonzept beinhaltet eine Just-insequence-Anlieferung sowie das Leergut- und Qualitätsmanagement. Der Kunde konnte sich ganz auf den Aufbau seiner Montagelinien für die Hochvoltspeicher konzentrieren. Die vorgelagerte Komponentenmontage haben wir ihm abgenommen und konnten so einen wichtigen Beitrag zur Verkürzung der Time-to-Market leisten.
Am gleichen Standort übernehmen wir die Instandhaltungsarbeiten in der Batteriemontage. Beim zweiten Werk haben wir unsere Erfahrungen bereits während der Errichtung mit einbringen können. Die beiden Aufträge für Instandhaltungsaktivitäten für Batterielinien sind die ersten ihrer Art in Europa, die von einem technischen Dienstleister übernommen wurden. Heute betreuen wir bereits acht Batterielinien.
Wie profitiert die Werksleitung von der Zusammenarbeit mit Industriedienstleistern?
Zunehmend entstehen neue Werke für die Batteriezellenfertigung, immer mehr auch in Westeuropa, sowohl von asiatischen und amerikanischen Herstellern als auch – und immer mehr – von europäischen Unternehmen. Und diese haben klare Kriterien: Nachhaltigkeit in der Supply Chain, räumliche Nähe zu den Fahrzeugmontagewerken, CO₂-neutrale Produktion, Zugang zu qualifiziertem Personal, Kenntnis der lokalen Gesetzgebung und eine schnelle Hochlaufkurve. Viele dieser Unternehmen sind neu in Ländern wie Deutschland oder auch Frankreich. Sie müssen dann in kurzer Zeit nicht nur die Produktionsanlagen aufbauen, sondern auch 1.000 bis 2.000 Mitarbeiter qualifizieren, Fertigungs- und Prüfprozesse einführen. Time-to-Market ist hier alles! Da nehmen erfahrene Industriedienstleister wie Leadec, die bereits eigene Systeme und Tools für den Aufbau von technischen Dienstleistungseinheiten in Greenfield-Werken haben, viele Aufgaben ab.
Und was bedeutet Outsourcing auf der Kostenseite?
Heute geht es in den Medien oft noch um Themen wie Schnellladefähigkeit, Energiedichte und Reichweite. Um die Nachfrage nach batteriebetriebenen Fahrzeugen weiter zu steigern, geraten die Fahrzeugkosten und damit vor allem auch die Produktionskosten der Hochvoltspeicher unter Druck. Hier rücken die Automatisierung und die Instandhaltung in den Blick. Zwar machen die Material- und Anlagenkosten den größten Teil der Herstellkosten einer Batteriezelle aus, zusammen etwa 70-80 Prozent. Dieser Anteil wird jedoch unabhängig vom Standort des Werks durch die Weiterentwicklung der Werkstofftechnologien in den nächsten Jahren weiter deutlich sinken. Signifikante Kostenbestandteile bleiben dann die Lohn- und die Instandhaltungskosten. Innovative Automatisierungslösungen und Instandhaltungskonzepte für die neuen Fertigungs- und Montagetechnologien wie der Einsatz von Smart Factory Analytics dürften hier die Wettbewerbsfähigkeit europäischer Batteriezellenwerke deutlich verbessern.
Welche Kompetenzen werden bei Ihnen derzeit besonders nachgefragt?
Die meisten Projekte haben wir im Moment bei der Serienplanung von Montageprozessen, der Planung und Umsetzung spezieller Brandschutz- und Havariekonzepte und bei Tätigkeiten in der Qualitätssicherung. Letztere betreffen den Anlieferbereich von Modulen, die einzelnen Montageschritte im Rahmen des Korrosionsschutzes, das fachgerechte Ausschleusen oder den Abtransport von NOK-Batteriesystemen aus dem Werk. Seit zwei Jahren bekommen auch Kompetenzen in der Versorgungslogistik der Werke mit Batteriesystemen und Antriebskomponenten einen immer höheren Stellenwert.
Wie sehen Sie die Zukunft des Batteriestandortes Europa?
Bei der Batteriezellenfertigung sind bislang die asiatischen Unternehmen mit ihren asiatischen Fertigungsstätten noch wesentlich weiter in der Industrialisierung der Fertigungstechnologien. Jetzt zeigt sich allerdings, dass die räumliche Nähe zu den europäischen Produktionswerken der Automobilhersteller mögliche Nachteile in der Produktionseffizienz immer mehr aufwiegt. Gerade im letzten Jahr hat die politische Diskussion über den Batteriestandort Westeuropa, vor allem Deutschland und Frankreich, noch einmal deutlich an Intensität gewonnen. Zunächst hatten vor allem die asiatischen Hersteller angekündigt, neue Kapazitäten zur Batteriezellenproduktion in Europa aufzubauen. Inzwischen haben aber auch europäische und amerikanische Unternehmen damit begonnen, in Europa neue Werke zu errichten. Erwartet werden bei der Batteriezellenfertigung neue Produktionskapazitäten über 250 GWh/a allein bis 2025 und dann noch einmal mehr als eine Verdoppelung bis 2030. Gleichzeitig bauen die europäischen Chemieunternehmen hierzulande Kapazitäten auf. Es ist sehr viel in Bewegung
Bricht jetzt das Goldene Zeitalter für den Industrieservice an?
In der Tat haben jetzt Industriedienstleister wie Leadec eine besondere Chance, ihre Erfahrungen aus den verschiedenen Wellen der Entwicklung der Automobilproduktion einzubringen und den Transformationsprozess zu unterstützen. Der Industrieservice wird sich weiter professionalisieren. Mit den neuen Fertigungs-, Montage- und Prüftechniken wird sich der Trend zu Smart Manufacturing und damit auch zu Smart Services gerade bei der Herstellung von Batteriezellen und -modulen weiter verstärken. Unsere Strategie der integrierten technischen Dienstleistungskette vom Engineering über die Automatisierung und die Produktionsinstandhaltung bis hin zur Produktionslogistik und zum Facility Management bringt uns nun Vorteile dabei, unseren Kunden für eine schnelle Time-to-Market besondere Lösungen anzubieten. Leadec sieht sich hier sehr gut aufgestellt.