Die Rechnung ist einfach: Je sauberer und sortenreiner die Abfälle sind, desto leichter lassen sie sich aufbereiten und verwerten. Das spart Energie und schont vor allem die Ressourcen. Doch in der Realität trennen viele Menschen ihren Müll falsch. Und wenn der Abfall erst einmal chaotisch auf dem Förderband eines Wertstoffhofes liegt, ist es zu spät. Dann müssen Maschinen ran: Sortieranlagen, die den Abfall so vorbereiten, dass er zum Beispiel verbrannt werden kann. Denn die thermische Abfallbehandlung bietet die Möglichkeit, das Abfallvolumen effektiv zu reduzieren und gleichzeitig Energie zurückzugewinnen. Der größte Teil der anfallenden Abfälle – zum Beispiel aus Haushalten – wird bei Temperaturen von bis zu 1.200 °C verbrannt. Die Hitze, die bei der Verbrennung entsteht, erzeugt Wasserdampf. Der wiederum treibt über Turbinen nachgeschaltete Generatoren an und erzeugt so Strom.
Abfall ist nicht gleich Abfall
Was nicht ins Feuer gehört, sind Kunststoffe. Sie können recycelt und so der Kreislaufwirtschaft wieder zugeführt werden. Um diesen Wertstoff vorab vom Restmüll zu trennen, werden daher automatische Sortieranlagen eingesetzt, die Kunststoffe gezielt aussortieren. Für die Nachrüstung einer solchen Vorschaltanlage in einem großen Recyclinghof realisiert und konzipiert Leadec in Zusammenarbeit mit einem deutschen Anlagenbauer die Steuerungstechnik derzeit.
Die besondere Herausforderung bestand darin, dass der Umbau bei laufendem Betrieb erfolgt – also nur kurze Stillstandszeiten am Wochenende zur Verfügung stehen, um die komplexe Automatisierungstechnik zu erweitern. Seit 2021 fällt der Entsorgungssektor zudem unter das IT-Sicherheitsgesetz 2.0, das unter anderem Anforderungen an die Cybersicherheit für kritische Infrastruktur regelt. „Wir haben die Steuerungstechnik der Anlage daher so ausgerichtet, dass sie entsprechend den Anforderungen des Bundesamtes für Sicherheit in der Informationstechnik BSI nun KRITIS-konform ist“, erklärt Frank Seifert, Leiter Business Development für den Bereich Automation bei Leadec. „Denn die Vorschaltanlage mit der Kunststofftrennung ist essentiell für die Abfallentsorgung für mehrere Millionen Menschen einer deutschen Großstadt.“
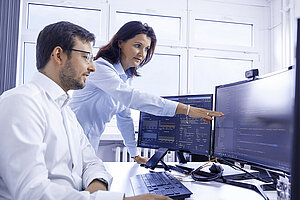
Laser an und sortiert ins Feuer
Um alle Wertstoffe auszusortieren, wird der Abfall zunächst in einer gleichmäßigen Schicht auf den Förderbändern verteilt, um eine genaue Erfassung und Analyse zu ermöglichen. Spezielle Laser, die über dem Abfallstrahl angeordnet sind, erzeugen einen intensiven Lichtstrahl, der auf die Oberfläche des Kunststoffabfalls gerichtet ist. Das Laserlicht interagiert mit dem Kunststoff und erzeugt ein charakteristisches Spektrum von reflektiertem oder gestreutem Licht.
In Echtzeit analysiert das System diese Informationen, vergleicht sie mit vordefinierten Mustern und klassifiziert die gescannten Materialien. Erhält ein Aktor am Förderband dann die Information, dass sich ein Kunststoff auf dem Band befindet, öffnet er gezielt Schleusen und das Teil landet in einem separaten Auffangbehälter oder auf einem weiteren Förderband. „In solchen Anlagen werden mehrere tausend Tonnen Abfall pro Tag verarbeitet“, weiß Frank Seifert, „entsprechend fatal wäre eine Störung der Anlage und im schlimmsten Fall ein Stillstand.“ An die Automatisierungstechnik werden daher höchste Anforderungen gestellt, um die Komplexität des gesamten Aufbereitungsprozesses zu erfassen und die Arbeitsschritte perfekt aufeinander abzustimmen.
„Green Factory Solutions“ für Schonung der Ressourcen
Im Rahmen der „Green Factory Solutions“ bietet Leadec unter anderem die Automatisierung solcher Recyclinganlagen an. Frank Seifert: „Unser Beitrag liegt im technischen Know-how, dem verfahrenstechnischen Verständnis und damit in der Möglichkeit, Abfälle durch Recycling in neue Ausgangsstoffe umzuwandeln. So müssen keine neuen Rohstoffe abgebaut werden und es wird nur genau der Abfall verbrannt, der an anderer Stelle nicht recycelt werden könnte. Das spart Energie und reduziert negative Auswirkungen auf die Umwelt.