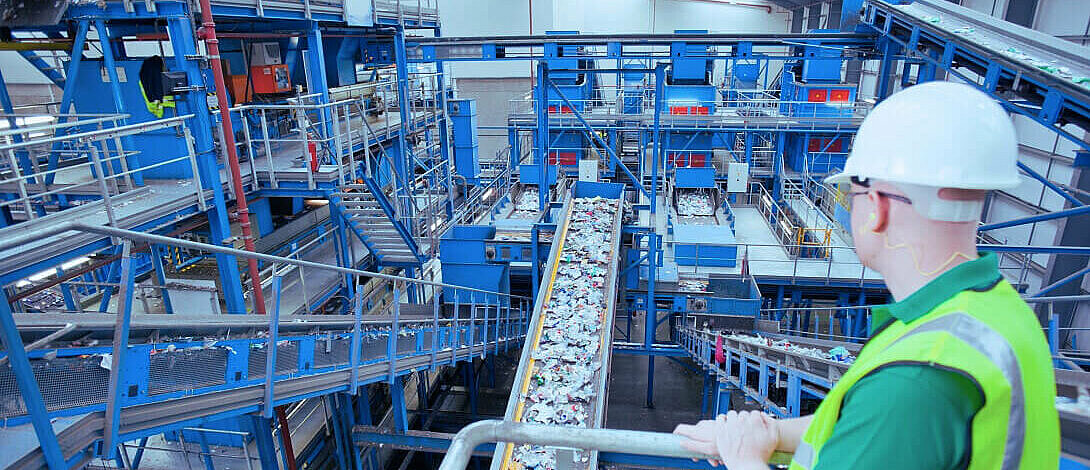
The calculation is simple: the cleaner and more sorted the waste, the easier it is to process and recycle it. This saves energy and, above all, conserves resources. But many people separate their waste incorrectly. And once the waste lies chaotically on the conveyor belt of a recycling plant, it’s too late. That’s when machines have to step in: sorting systems that prepare the waste so that it can be incinerated, for example. Thermal waste treatment offers the possibility of effectively reducing the volume of waste and recovering energy at the same time. Most of the waste generated – from households, for example – is incinerated at temperatures of up to 1,200 °C. The heat generated during incineration produces steam. This in turn drives downstream generators via turbines to produce electricity.
Not all waste is created equal
Plastics must not be incinerated. They can be recycled and thus returned to the circular economy. In order to separate this recyclable material from the residual waste in advance, automatic sorting systems are used that specifically sort out plastics. Leadec, together with a German plant manufacturer, is currently designing and implementing the control system for the retrofit of such a sorting system in a large recycling plant.
The particular challenge is that the conversion is carried out during ongoing operations, i.e., only short downtimes are possible at the weekend to expand the complex automation system. In addition, since 2021, the waste disposal sector has been covered by the German IT Security Act 2.0, which, among other things, regulates cybersecurity requirements for critical infrastructure. “We have therefore adjusted the plant’s control system so that it now complies with the regulations for critical infrastructure of the German Federal Office for Information Security (BSI),” explains Frank Seifert, Head of Business Development for the Automation & Engineering unit at Leadec. “After all, the plastic waste separation system is essential for waste disposal for several million people in a major German city.”
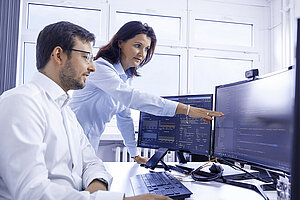
Laser on, sort out, and into the fire
In order to sort out all recyclables, the waste is first distributed in an even layer on the conveyor belts to enable accurate detection and analysis. Special lasers positioned above the waste create an intense beam of light directed at the surface of the waste. The laser light interacts with the plastic to produce a characteristic spectrum of reflected or scattered light.
In real time, the system analyzes this information, compares it with predefined patterns and classifies the scanned materials. If an actuator on the conveyor belt then receives the information that plastic is on the belt, it opens sluices and the part lands in a separate collection container or on another conveyor belt. “In such plants, several thousand tons of waste are processed every day,” Frank Seifert knows, “a malfunction of the plant and, in the worst case, a shutdown would be fatal.” The highest demands are therefore placed on the automation technology to take into account the complexity of the entire treatment process and to perfectly coordinate the work steps.
“Green Factory Solutions” to conserve resources
As part of its “Green Factory Solutions,” Leadec offers, among other things, the automation of such recycling plants. Frank Seifert: “Our contribution lies in the technical know-how, the understanding of process engineering and thus the possibility of converting waste into new feedstock through recycling. This means that no new raw materials have to be mined and only precisely that waste is incinerated which could not be recycled elsewhere. This saves energy and reduces negative impacts on the environment.”
You may also be interested in the following articles:
Are you interested in our services?
Please send us your request. We would be happy to hear from you.
*mandatory