The Golden Age of Industrial Services?
Lithium-ion battery, fuel cell or biogas - which is the technology of the future?
Dr. Christoph Jaschinski: Batteries, especially optimized lithium-ion batteries, are now seen worldwide as a key technology for electric vehicles. Many manufacturers and suppliers are also experimenting with other fuels and drive technologies, such as hydrogen in combination with fuel cells or synthetic fuels. But it is becoming clear that, at least in the medium term, the focus for passenger cars will be on vehicles with lithium-ion batteries. By 2030, for example, more than 4.5 million electric vehicles are expected to be produced annually in Germany alone. Recent estimates suggest that over 4.6 million battery-powered vehicles will be sold in Europe as early as this year. This growing demand continues to pose major challenges for the industry. It starts with the planning and ramp-up of new plants, continues with the transformation of existing plants, on to efficient and cost-effective service models and ends with the supply chain. This is where specialized technical service specialists are needed - with expertise in all aspects of modern factory organization.
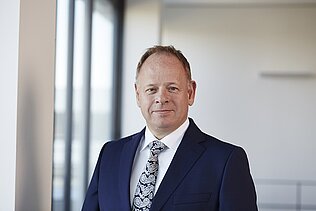
Head of Global Business Development, Leadec Group
What does such a service specialist have to bring along?
The requirements differ depending on the stage of the value chain. In the case of vehicle assembly, i.e., the “marriage” of battery and the car body, it is primarily a matter of implementation know-how or planning and operating expertise for the complete intralogistics of the electric vehicle batteries. The situation is different for battery pack assembly plants. Here, special planning competencies are needed in assembly technology, automation, and analysis methods, but also in quality assurance and control. The actual production of battery cells is particularly demanding. Europe lacks process knowledge in this area, and manufacturing technologies are still changing very rapidly. For example, the industry demands knowledge about smart factory analytics, agile working or plant technologies that can often only be developed together with plant manufacturers.
What experience does Leadec have?
We have references for testing and in large-scale production through projects in Germany, Poland, and the US. They have shown that manufacturers are primarily interested in technical services. Engineering, maintenance of new assembly lines, services for pre-assembly, and supply logistics are at the top of the list. One example: Among others, Leadec cooperates with a subsidiary of Daimler AG. Sophisticated lithium-ion batteries for plug-in hybrids or all-electric vehicles are built in Kamenz near Dresden.
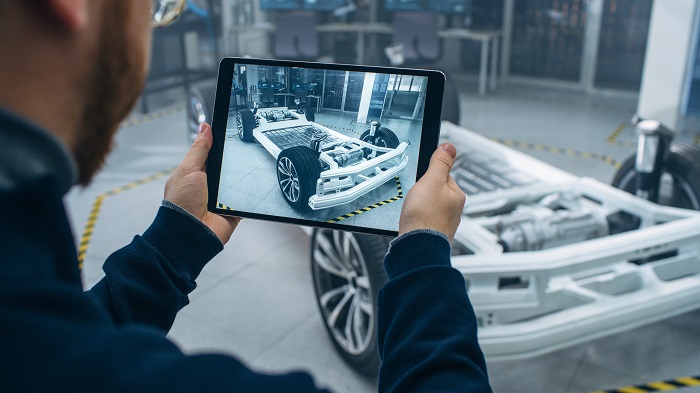
Within a few months, Leadec planned and implemented a service model for the pre-assembly of different battery pack cases here at its own site outside the factory premises. The innovative supply concept includes just-in-sequence delivery as well as empties and quality management. The customer was able to concentrate entirely on setting up its assembly lines for the electric vehicle batteries. We took over the upstream component assembly and were thus able to make an important contribution to shortening the time to market.
At the same location, we are responsible for the maintenance work in the battery assembly line. At a second plant, we were able to contribute our experience already during construction. The two orders for battery line maintenance activities are the first of their kind in Europe to be taken on by a technical service specialist. Today, we are already looking after eight battery lines.
How does the plant management benefit from the cooperation with industrial service specialist?
Increasingly, new plants for battery cell production are being built, more and more also in Western Europe, both by Asian and American manufacturers and more and more by European companies. And they have clear criteria: sustainability in the supply chain, proximity to vehicle assembly plants, carbon neutral production, access to qualified personnel, knowledge of local legislation, and a fast ramp-up curve. Many of these companies are new to countries such as Germany or France. They then not only have to set up production facilities in a short time, but also train 1,000 to 2,000 employees and introduce manufacturing and testing processes. Time to market is everything! Experienced industrial service specialists such as Leadec, who already have their own systems and tools for setting up technical service units in greenfield plants, take on many of the tasks.
And what does outsourcing mean on the cost side?
Today, the media often still focus on topics such as fast-charging capability, energy density, and range. In order to further increase the demand for battery-powered vehicles, the vehicle costs and thus, above all, the production costs of electric vehicle batteries are coming under pressure. This is where automation and maintenance come into focus. It is true that material and equipment costs account for the largest share of the manufacturing costs of a battery cell, about 70 - 80 percent in combination. However, this proportion will continue to fall significantly over the next few years due to the further development of materials technologies, irrespective of the location of the plant. Significant cost components will then remain in the shape of wage and maintenance costs. Innovative automation solutions and maintenance concepts for the new manufacturing and assembly technologies, such as the use of smart factory analytics, should significantly improve the competitiveness of European battery cell plants.
Which skills are currently in particular demand at your company?
Most of our current projects entail series planning of assembly processes, the planning and implementation of special fire protection and emergency concepts, and quality assurance activities. The latter relate to the module delivery area, the individual assembly steps as part of corrosion protection, the professional discharge or the removal of NOK battery systems from the plant. For the past two years, competencies in the supply logistics of the plants with battery systems and drive components have also become increasingly important.
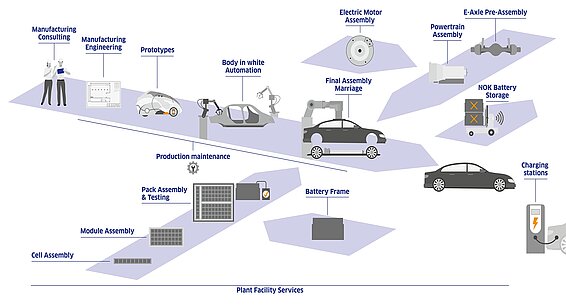
How do you see the future of Europe as a battery production location?
In battery cell production, Asian companies with their Asian production facilities have so far been much further ahead in the industrialization of manufacturing technologies. However, it is now becoming apparent that the geographical proximity to the automobile manufacturers’ European production plants is increasingly outweighing possible disadvantages in production efficiency. In the past year in particular, the political discussion about Western Europe as battery production location, especially Germany and France, has once again become much more intense. Initially, Asian manufacturers had announced that they would build new capacities for battery cell production in Europe. In the meantime, European and American companies have also begun to build new plants in Europe. New battery cell production capacities of over 250 GW h/a are expected by 2025 alone, and this figure is expected to more than double by 2030. At the same time, European chemical companies are building capacity in Germany. There is a lot going on.
Is the golden age of industrial services dawning?
Indeed, industrial service specialists like Leadec now have a special opportunity to contribute their experience from the various waves of automotive production development and support the transformation process. Industrial service will continue to professionalize. With the new manufacturing, assembly, and testing technologies, the trend towards smart manufacturing and thus also smart services will continue to intensify, especially in the production of battery cells and modules. Our strategy of an integrated technical service chain from engineering to automation, from production maintenance to production logistics, and facility management now gives us advantages in offering our customers special solutions for a fast time to market. Leadec considers itself to be in an excellent position to deliver on this count.
Want to find out more about Battery Production?
On a total of 43 pages, the white paper provides an overview of battery production in Germany and Europe and highlights how this is changing the demands on factories.