Leadec maintains electrical and hydraulic equipment, HVAC, cranes and welding equipment, and provides technical and infrastructural cleaning at the Mercedes-Benz SBdC plant. In total, the nearly 400-member team is responsible for around 10.000 installations on the one-square-kilometer site.
The Leadec.os platform automatically generates an order at the defined time for the facility management tasks. The Leadec team then creates a work order and assigns it to technicians on site on their tablets. The Leadec employees perform the required work and report completion via the tablet. The progress of each job can be tracked digitally in real time via reports and dashboards.
In addition, the Leadec team receives orders for short-term requirements via the Leadec.os platform in real time, allocates the needed personnel and immediately takes action.
“Leadec.os provides our customer with more clarity in the data related to facility management. They use this data to plan the next steps,” says Pedro Salviano Franca, Contract Manager at Leadec Brazil.
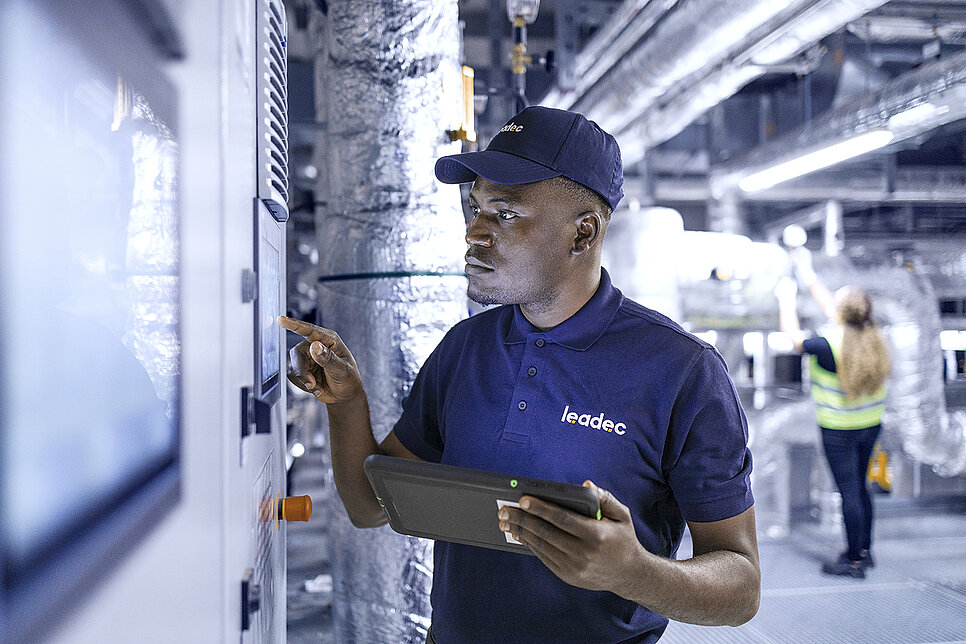
The Leadec team receives orders for short-term requirements via the Leadec.os platform and immediately takes action.