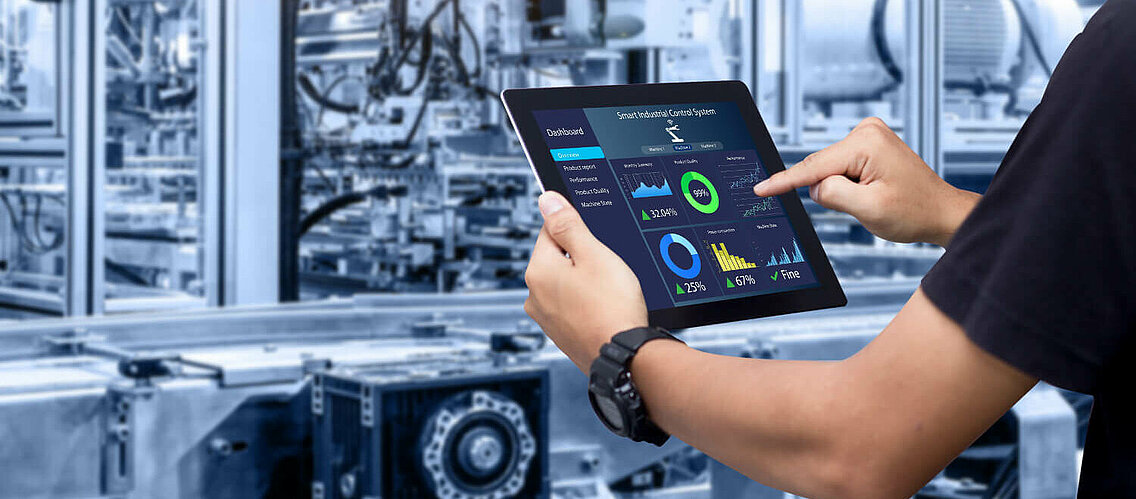
Leadec is rigorously converting to cloud technology. Its own platform, Leadec.os, is a cloud-based solution that digitally maps all stages in the service process from quotation to provision of the service to documentation and billing. The platform can be connected to the cloud technologies of other providers. One current extension is the IoT home cloud, which additionally enables industrial IoT applications. Leadec can structure and visualize recorded data and use artificial intelligence to draw conclusions and initiate activities based on them. Supported applications include, for example, monitoring of aggregates in machining centers or tracking of welding seams, described in more detail below.
Real-Time Digital Inspection of Weld Seams
The digital system records quality-relevant welding process data via a communication interface from the welding power sources and documents them in real time in the higher-level database, either “on-premise” or in the cloud. There, an algorithm evaluates the data by means of defined parameters, often linked with data from other QA systems. The monitoring results enable constant feedback to the automation process for the system so that operators can promptly respond to potential quality problems. The weld seam inspection can be integrated into new systems or retrofitted into existing ones and monitors both robot-supported welding systems and manual welding stations. The system offers various monitoring types, for example, envelope-based corridors for typical arc parameters such as welding current, welding voltage, wire feed speed, and so on. With the continuous quality inspection, every single part can be inspected and the need for destructive component testing, manual rework, and inspection is lowered. In addition, the software offers the possibility of predictive maintenance of connected systems because motor currents and, e.g., torques in the wire feeder can be digitally recorded with it.
AI training in two weeks
Leadec implemented another application in plants in India and Germany. Pumps and compressors in the machining facilities there were equipped with vibration sensors to enable analysis of continuously recorded data. Predictive maintenance was the primary goal here. The data are processed in the sensors and analyzed in the IoT home cloud to yield usable information.
The first step in this process is to detect anomalies and then send out alerts. The second step is to understand why an anomaly occurs and, if possible, derive the causes of the error from the recorded data. An industrial machine learning application is capable of selecting relevant data, filtering them, recognizing patterns in them, and working out possible solutions. In the application, an AI algorithm for processing the vibration data from the machines was rolled out. Once the system was verified, it could generate individual threshold values from learning data from the first two weeks after maintenance or installation of the machine. For this, the algorithm creates a so-called mother condition that describes the individual machine behavior. The current sensor data are then continuously compared with this original condition. Any data outside the boundaries causes the IoT application to trigger an alert.
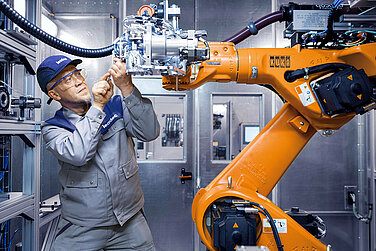
Developing future business models
Every time there is an alert, the manager can plan, track, and report on the maintenance activities. For this, the alert information is mapped in real time via the Leadec.os digital platform. This integration allows the service provider to build up a database of all systems supported worldwide. This form of data visualization, the accumulated knowledge about the processes and data for comparison, can also serve as the basis for new business models. Service-level agreements (SLAs) can be costed more reliably, and even availability guarantees can be offered. In a further stage, service providers can even assume full responsibility for the machines and facilities or their provision for manufacturing processes. However, this requires an ecosystem that connects the machine manufacturer, software specialists, system integrators, and people with manufacturing know-how. This is also why Leadec is working on the development of new business models in the form of end-to-end service offerings within the framework of the Fraunhofer ICNAP study entitled “Monetizing Industrial Data.”