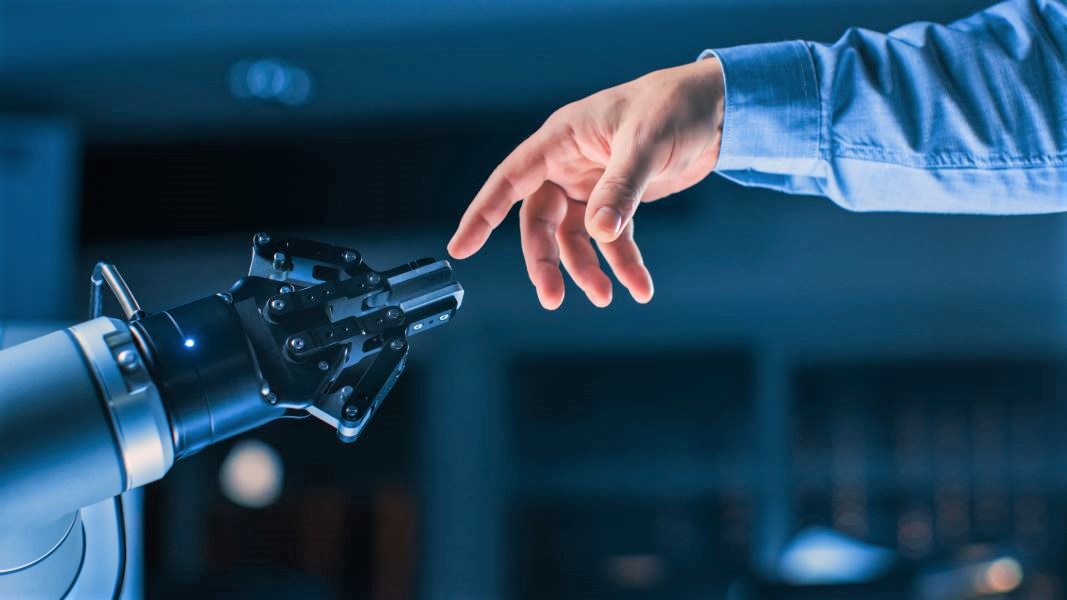
The bulky robot arm that was busily assembling parts just a moment ago suddenly freezes. The door to its glass cage is open and integrated safety solutions have ensured immediately that the machine colleague stops its work. Outside, automated guided vehicles whiz by, carrying goods from A to B. Clearly, we are in a smart factory. Leadec, for example, not only takes care of the planning and setting up of such modern factories but also of the maintenance of entire assembly lines. What is striking here is that assembly in the modern factory in particular is characterized by a high degree of automation, with humans and robots increasingly working hand in hand with one another. Behind this is the concept of human-robot collaboration (HRC). This generation of “cobots” – i.e., collaborating robots – is considered one of the central tools in a smart factory.
Fair division of labor
With HRC, all actors can move more freely, processes and work steps do not have to be interrupted. In addition, when man and machine share one and the same workstation, less space and protective equipment are required. This saves time, money and makes manufacturing more flexible overall. In addition, the workload of humans is reduced by the fact that machine colleagues perform dangerous or ergonomically uncomfortable work. Whether it’s servicing a machine upside down, performing complex precision work or lifting heavy loads over small distances. This not only protects health, but it also ensures a plus in occupational safety. And the human being? As long as the machine does the back-breaking work, workers focus on complex tasks that require their expertise.
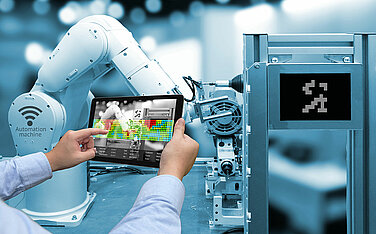
Safety is a priority
A robot arm can be repaired, a human arm is incomparably more at risk. While in the past the machines were therefore kept safe, today intelligent solutions directly on the robot even enable hazard-free mutual contact. The key is powerful sensors and cameras that not only allow detailed assembly tasks but also ensure that the cobot does not injure the human. In the event of unwanted contact, for example, the robot can automatically slow down its speed, reduce its radius of action or even stop in an emergency by means of an algorithm.
Artificially intelligent
Manufacturers of robots, such as ABB or Kuka, are also working on learning systems for their products. For example, by interacting with their human colleagues, the cobots are supposed to learn from them, to correctly assess dynamic movements in the production area and to draw conclusions about their behavior. The aim is to give the robot the freedom to move as quickly and energy-efficiently as possible while at the same time complying with stringent safety requirements. Work is also already underway on intelligent automatic guided vehicles (AGVs) in the field of intralogistics. If an unexpected obstacle gets in the way of these – for example, a human being on the way to his or her lunch break – then it’s “STOP!”, which abruptly ends a transport process. Artificially intelligent AGVs, on the other hand, attempt to predict the behavior of moving objects through independent learning and react accordingly. Be it by slowing down or taking evasive action. For a safe coexistence.
You might also be interested in:
Automation & Engineering - More efficiency with robCONTROL
Article in Pulse - Leadec - A Software Developer?