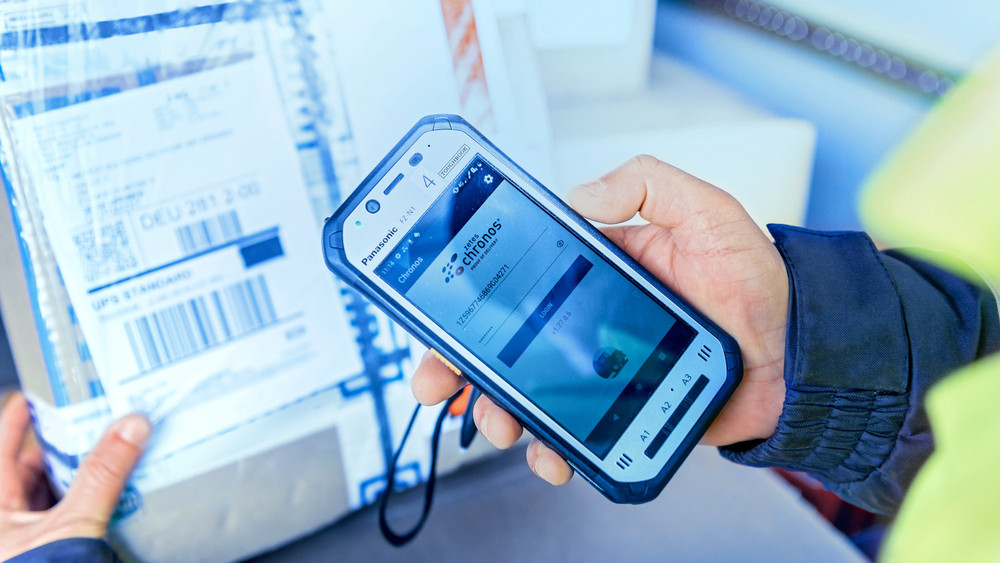
The socalled ‘non-production material’ (NPM) is located in dedicated warehouses across an extensive factory site in Bremen to be called up on demand by numerous departments. The spectrum of around 50,000 different articles ranges from work gloves and tools to welding robots. If these things are missing, production comes to a stop – and that’s costly”, says Alexander Bölken, head of logistics at Leadec’s Bremen location.
Along with accurate on-time delivery, client demands maximum transparency of open and closed processes. The sequence of delivery points can be viewed online by the customer, as can the time and location of the handover of goods. Last but not least, the monthly invoices are also easily traceable and controllable on the basis of a digital statement of services.
This is made possible by ZetesChronos, an electronic proof-of-delivery software.
Intuition instead of a manual
The key elements of the solution include the proof-of-delivery app and a cloud based management visibility platform incorporating multiple various dashboards for capturing, planning, monitoring and analysing deliveries. Based on this, two planners at the site in Bremen generate loading lists out of the system for the delivery vehicles. Each truck makes up to three trips per day, carrying 50 to 70 returnable containers and pallets, as well as around 120 to 200 parcels, from the NPM warehouses to the individual departments.
The delivery process begins with sending the trip data to the mobile scanners of the drivers. The display guides the driver through all orders and procedures. Loading errors are immediately noticeable because each shipment is first scanned and compared to the planning data. Discrepancies are signalled to the driver both audibly and visually. “Every standard order must be delivered within 24 hours”, explains Bölken. For urgent spare parts there is an express delivery service, which takes only 45 minutes on a special route.
Correct placement
When unloading, the barcode of the delivery point is scanned. There is also a photo function: the driver must photograph the unloaded pallets or containers to document correct delivery. The photos also serve as a delivery receipt and can be retrieved by the customer via the ZetesChronos online platform, the same as all other delivery data and times. “Every standard order must be delivered within 24 hours”, explains Bölken. For urgent spare parts there is an express delivery service, which takes only 45 minutes on a special route.
Extremely low error rate
After the first few months, Leadec draws a positive conclusion. Of the approximately 15,000 shipments transported up to now, there were only ten incorrect deliveries, corresponding to an error rate of less than 0.15 per cent. “The processes and control mechanisms defined by the system result in an extremely low error rate, leading to very high customer satisfaction,” says Alexander Boelken.
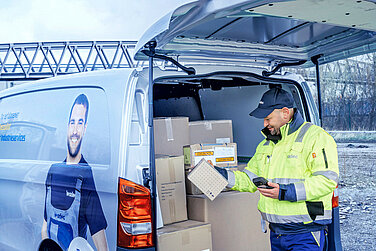
You might also be interested in:
Leadec services "Logistics"
Press release "Optimized Logistics Planning Thanks to Simulations By Leadec"