“The Future Belongs to Integrated Facility Management"
Is Integrated Facility Management really an evolution and not just hype?
Christoph Jaschinski: Definitely the first! But why is Integrated FM becoming more and more popular? Some advantages are obvious. An Integrated FM model bundles a wide range of services from a single source. Companies have just one central contact who coordinates everything across sites, regions, or countries. They can rely on centralized processes and standards. This reduces complexity and companies can focus on their core competencies. Integrated FM also helps to increase plant availability and create a better workplace experience.
At first, this sounds very general and can apply to different services or branches.
Not all Integrated FM is the same. Many service providers come from traditional facility management focusing on buildings. However, there are completely different requirements in manufacturing. In factories, it’s all about asset optimization, higher productivity and mitigating the losses incurred by downtime. To do this, service providers need a depth of technical understanding, must know every plant component and the conditions on site, and understand the special production challenges.
This is where another current issue comes into play: industrial companies are having major problems recruiting and retaining qualified people with technical skills over the long term. Outsourcing to a specialized service provider is one way to counter the lack of skilled staff.
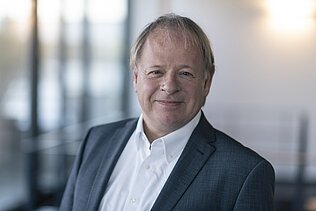
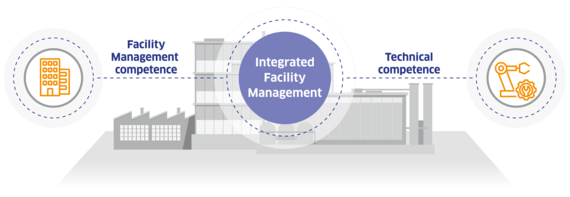
What does it take to implement an Integrated FM model?
Taking facility management to the next level by implementing an Integrated FM model means a more strategic alignment of the requested outcome of the services in scope. Tailored Integrated FM concepts manage technical and administrative processes equally.
The basis for this is sound technical know-how and consideration of the entire site, not just individual orders. Production is viewed as a holistic end-to-end process, where the risk of failure must be minimized, and the whole life cycle of the facilities must be simultaneously maximized. This is the only way to create an optimal Integrated FM package that includes both hard and soft FM services.
Is there a “golden rule” for how it works ideally?
Integrated facility management is a model that often cannot be achieved in one step. The specifications and requirements of the sites are usually very different. Most often, companies start by bundling services into packages before fully outsourcing all FM activities to one service provider. Or Integrated FM is first introduced at one site and then expanded step by step across several sites, regions, in one country and finally even across countries. By switching to an Integrated FM model, companies can achieve savings of up to 25% over the contract period.
Not only does the level of Integrated FM maturity vary among companies, but there are also differences between sectors. While the awarding of Integrated FM services has been widespread and very mature for some time in the consumer goods or pharmaceutical industries, for example, Integrated FM is only now gaining momentum in the automotive sector. We are convinced that the future belongs to integrated facility management.
The initial 5 steps for a successful Integrated FM
- Start bundling services into packages and find a reliable outsourcing partner with the right set of skill
- Establish a roles and responsibilities matrix and utilize kick-off meetings to get team engagement
- Identify the main site requirements, but allow flexibility for the partner to deliver the right results
- Develop a contract model that meets your requirements and drives the right outcomes
- Use a CMMS system as the backbone for managing service performance and tracking KPIs