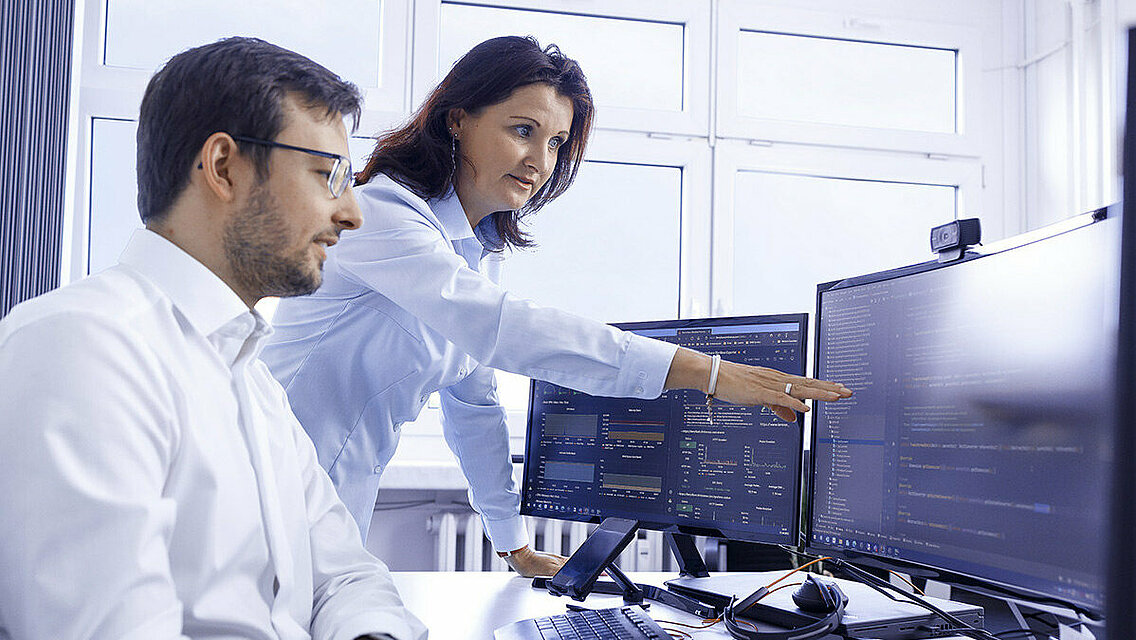
Almost ten years ago, Fraunhofer IKTS and battery manufacturer Altech began developing a new solid-state battery. Since then, the project has made significant progress, and the technology is now ready for industrial product development. A suitable location has also been identified: a new facility for these high-performance batteries is set to be built at the Schwarze Pumpe industrial park in Saxony, Germany—home to Altech’s operations. But the road to sustainable batteries is a long one: The feasibility study was successfully completed in spring 2024. Leadec is responsible for providing engineering services to translate the process industrialization into a comprehensive factory planning effort. “Leadec brings extensive experience in battery manufacturing and will play a key role in driving the final feasibility study for the commercialization of CERENERGY® sodium-alumina solid-state batteries,” said Uwe Ahrens, Executive Board Member of Altech Advanced Materials AG, at the project launch in 2022.
“Altech approached Leadec because they were looking for a partner to handle production planning,” says Gernot Herwig, Senior Sales Manager at Leadec Automation & Engineering. But that was just the beginning.
Leadec initially took on project administration, preliminary design, concept planning, as well as tender management and project coordination. In the areas of planning, process engineering, and plant construction, we’re coordinating the work of more than 40 selected suppliers. “Leadec is ready to help make Germany’s first solid-state battery factory a reality. We could get started immediately once the necessary permits are in place,” Gernot Herwig says with confidence.
Progress has already been made: Altech recently announced that the environmental and construction permits for the battery factory have been granted.
Initial target: 100 MWh per year
The production plant planned by Altech Group is expected to produce 10,000 battery modules per year, each with a capacity of 10 KWh. There are many possible applications for the solid-state batteries. The batteries will be installed in stationary energy storage systems, for example for renewable energies (wind, solar), as a component of the charging infrastructure for e-vehicles and in industry. Batteries also serve as energy storage in private households to provide a buffer between power generation and power consumption. And last but not least, electricity suppliers can avoid peak load capping in their megaparks.
Components conserve resources
The sodium-aluminum oxide solid-state batteries are particularly compelling because of the raw materials used. Saline is mainly used, with small amounts of nickel. This makes the batteries fire- and explosion-proof and at the same time easy to store. Added to this are a service life of around 15 years and estimated 40% lower production costs compared with lithium-ion batteries.
Battery production know-how
Leadec is involved in several battery manufacturing projects. Services range from the planning of production sequences, installation of the line and IT-based quality testing to the creation of prototype cells. For example, Leadec supported the establishment of Volkswagen's battery production at the Braunschweig site.
Video: Factory Talks about "Factory Planning"
State-of-the-art factories are expected to run more efficiently and place new demands on their operators. From networked production processes and a high degree of automation to close cooperation with customers and suppliers. What does this mean for the field of production planning?