Companies within the semiconductor industry place particularly high demands on logistics. In this interview, Gert Brandl, who works in account management for the semiconductor sector at Leadec and is the project manager in charge, explains why the company developed its own track and trace software for a customer and what makes it so special.
“A Shoebox Worth a Six-Digit Amount”
Why does a high-tech factory need track-and-trace software at all?
Many components within the semiconductor industry are extremely expensive, sensitive and difficult to procure. This means that the availability and precise handling of these materials play a key role. Components the size of a shoebox can be worth a high six-digit sum; if a component is lost or broken, it can take up to two years to procure a new one. The logistics software must therefore guarantee seamless documentation and tracking of materials to identify and avoid losses or stock shortages.
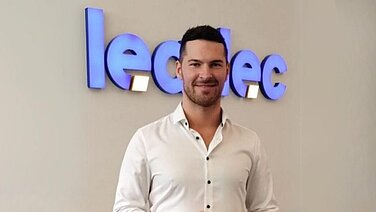
You have developed new software. What was the reason for this?
We provided various logistics services for a machine manufacturer in the semiconductor industry. Since 2021, we have been using logistics software that was originally developed for an automotive plant so that we can keep track of which component or material is where at all times. However, it could only be adapted to the special requirements of the semiconductor industry to a limited extent. Together with the customer, we therefore decided to develop a completely new software solution from scratch.
What were the particular challenges in the project?
In the semiconductor industry, issues such as the protection of sensitive data as well as building statics lead to a special construction method and therefore to very thick concrete walls. These make it difficult to set up a stable network. It requires special hardware – in our case the scanners – that can connect to all systems within the solid building shells.
What requirements does the software meet?
Seamless tracking of all components was very important to the customer. From ordering via the customer's SAP system, to delivery of the wares by a logistics partner and receipt of the goods at the factory. Leadec employees then confirm delivery of the materials by scan and transport them onwards. The delivered materials are shipped in various types of packaging - pallets, parcels, boxes and small packages - and have to be distributed across the extensive factory premises with 250 drop-off locations. Our teams use the software to plan the most efficient routes so that everything is in the right place within four hours of arrival at the latest. The handover can be done in person or via a drop-off authorization with image documentation. Via an online portal, the customer has full transparency at all times about where the individual items and components are located and what service we are providing at the plant.
What is your conclusion about the software and the project?
On the one hand, the project has shown how valuable the digitalization of logistics processes is in the semiconductor industry. The implementation was challenging, but we as a team were also able to prove that we have developed powerful and future-proof software by working closely with all partners.
You may also be interested in the following articles:
Are you interested in our services?
Please send us your request. We would be happy to hear from you.
*mandatory