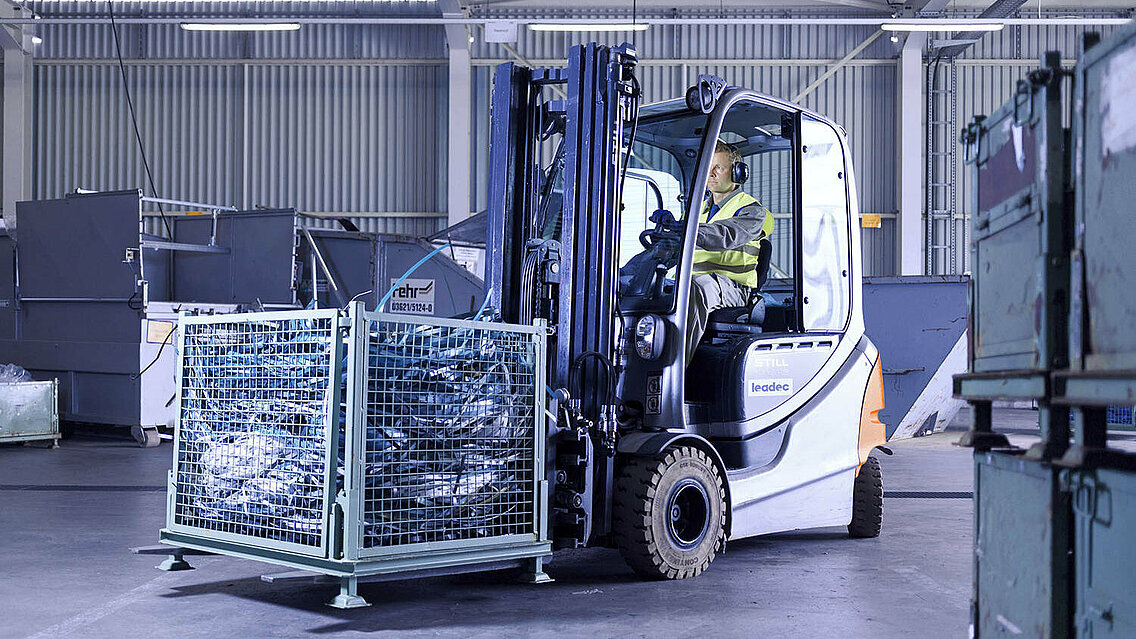
“Not all waste is the same” – this simple logic explains the different ways in which recyclable materials generated during the production of automobiles, for example, are handled. The spectrum ranges from plastic packaging, metals, and spray cans to adhesives, industrial waste, and paint sludge. And there is a suitable disposal solution for every type of waste. “The aim is not only to save disposal costs, but above all to make production more sustainable overall,” says Theodor Malcotsis, Team Leader Product Development at Leadec in Europe. “And this requires correct and comprehensive tracking of the disposed waste materials – completely digitally.”
Successful pilot project
In summer 2022, a large-scale pilot project was launched at an OEM’s plant, where the Leadec team is responsible for internal waste management, to test the digital solution, develop it further, and make it ready for regular use. “Initially, we provided around 190 waste containers and their respective locations with QR codes,” says Terence Gudat, Project Manager. “This allows routes to be optimized and the emptying of the individual containers with the respective types of waste to be recorded precisely.” All that is needed is a mobile infrared scanner that sends the data to the Leadec IoT platform, where it is processed in real time. “In the months leading up to fall 2023, we gained valuable insights from the project, adapted the system, and made it fit for regular operation from the start of 2024.”
Challenges in practice
In an ideal factory world, everything is in its place – in reality, routes are occasionally blocked, or containers are placed in a different location. Or mix-ups occur, which means that the types of waste in the containers have not been separated correctly. This has shown how important flexibility and adaptability of the systems are. At the same time, optimal preparation for recycling means more work in advance: the tracking system involves additional work steps, be it scanning the QR codes or the precise weighing of the individual container contents. But in the end, it’s the result that counts: a precise overview of where in the plant which waste is produced and in what quantity. This makes it possible to quickly identify potential savings in waste, increase the recycling rate, and adapt the waste services provided.
Regular operation with extended scope
“Because of the successful pilot project, we were able to prevail as provider of digital waste tracking in addition to our waste services,” says Theodor Malcotsis, adding that “we will now digitally manage the entire internal waste management for one part of the plant and have integrated the recording of other material flows such as mixed scrap containers, waste oils and hazardous substances into the system. The fact that we will also be setting up digital waste tracking at another plant speaks for the success of our approach.”