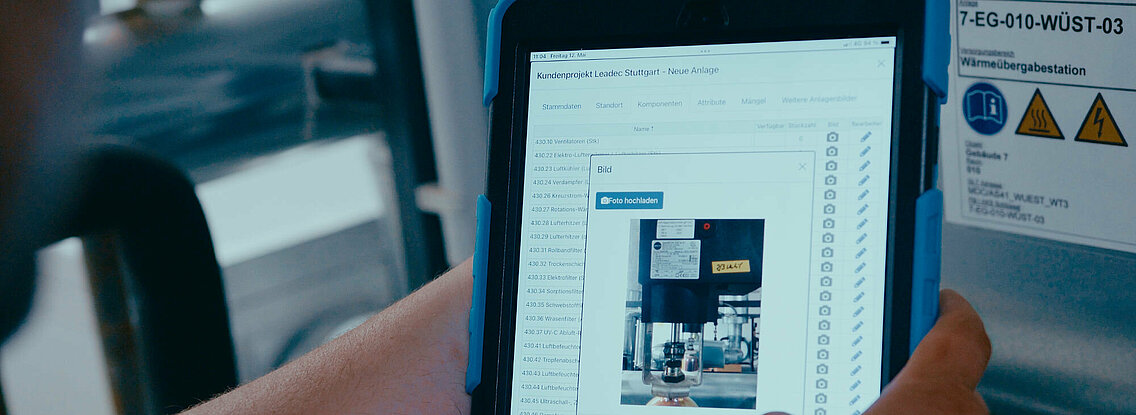
A factory contains thousands of technical assets – from fire doors and electrical distribution panels to ventilation systems. To ensure reliable maintenance, an up-to-date and detailed inventory list is essential. However, this is often where the challenge lies: reliable data is hard to find. This is particularly problematic when Leadec, as a technical service specialist, takes on a new contract. To address this, Leadec developed and implemented the LARA (Leadec Asset Recording & Administration) app in 2023. Since the end of January 2025, the new version has been successfully in use, and it is already clear: LARA 2.0 significantly outperforms its predecessor. It proves its capabilities in an automotive plant, where it is used for the detailed recording of around 1,500 assets.
What can LARA do?
The unique aspect of LARA 2.0 is that it is a complete in-house redevelopment. This massive project was carried out by teams from Leadec’s Smart Factory Group, Production IT, and Product Management Europe. "We worked together intensively to develop this new solution," says Astrid Lichtl-Dengel from the Smart Factory Group.
The redevelopment took key learnings from the first version into account. The new application is not only significantly faster and more powerful—especially in image processing—but also offers an improved user experience.
"In addition, we conducted a comprehensive practical test," says Stephan Hihn from Product Management Europe, explaining: “Employees who had never used LARA before tested the application under real conditions. This helped identify further important optimizations, such as a more logical sequence of steps for asset recording.”
Successful Rollout
LARA is currently running smoothly in its first real-world deployment at a customer site. "For the first two days, we were on-site to experience the users' reality firsthand, further improve usability, and correct any last minor errors," says Tim Trense from Production IT. He is pleased with the outcome: "We were able to demonstrate that LARA 2.0 is a significant improvement over its predecessor and takes Leadec's asset recording process to a new level." This means that the data recorded in LARA can be stored on the digital platform Leadec.os and used for upcoming tasks.
A Proprietary Cloud as the Foundation
The foundation for the new version of LARA is the Leadec Industrial Cloud. This fully self-developed cloud solution ensures optimal scalability and performance of digital services. "We want to be completely independent and rely on our own expertise and innovative strength," emphasizes Astrid Lichtl-Dengel.