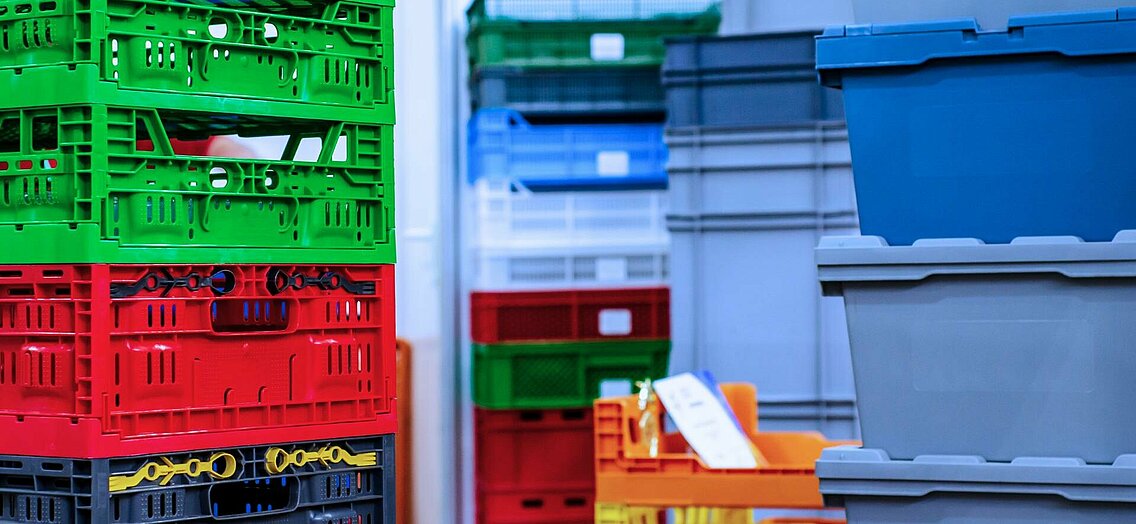
They protect the goods during transportation, ensure smooth delivery and, at best, are hardly noticed: packaging materials. At the same time, however, most expendable (cardboard box) packaging is thrown away after a single use. This is true in both private and industrial environments. Part of the Zero Waste Services that Leadec offers its customer at sites in Pune, Chennai and Bangalore, and across India wherever automotive OEM and Tier 1 and Tier 2 are present, are reusable packaging and crating solutions. “We clearly see the development of systems that meet the requirements of sustainability and modern production,” says Deepak Pandita, Head of Logistics at Leadec in India.
Packaging – more than a means to an end
Every day, small and large parts are transported from point A to point B in specially designed containers at the sites in Pune, Chennai and Bangalore and major auto hubs throughout India. There are no limits to the imagination, or rather, the customer’s wishes. Because there are so many individual requirements here, it has long been common practice for manufacturers to have their own containers that suppliers use. Ideally several times, but often only once. “Using packaging several times helps to reduce carbon footprints, minimize damage to parts, reduce turnaround time (TAT), and eliminate scrap, thereby reducing the overall supply chain costs,” says Deepak Pandita.
Rethinking reusable packaging
“Our approach to Zero Waste Services is now an end-to-end solution for packaging,” explains Pandita. This means container pooling, where several customers share standardized crates and reusable containers. The advantages are obvious: end-to-end supply chain management and multiple use. The standardized containers range from large, collapsible plastic containers with a load capacity of up to one metric ton to sturdy metal mesh containers, collapsible pallet sleeve systems, and small, handy crates.
Six steps to greater sustainability
These designs, together with Leadec’s services such as renting on a per-part basis or on a transactional basis, tracking, monitoring, and transportation, form a complete ecosystem for packaging logistics.
- Analysis of the components and selection of the appropriate container size and type
- Selection of the most suitable packaging solution for optimal fit of parts, for example wire mesh or plastic
- Design of customized inserts and separators, VFC trays and blisters to transport the parts in a shockproof manner
- Organization of logistics and storage for the packaging
- Cleaning, reconditioning, and maintenance of the packaging material
- Tracking and monitoring of the containers to obtain valuable data for optimizing logistics and providing MIS to customers
And what does this look like in practice?
The reusable containers are filled at a Tier 1 or Tier 2 supplier’s site (some of them by Leadec employees) and shipped to the OEM’s site or nearby transit warehouses. As soon as the parts have been removed, the Leadec team ensures that the empty container is returned to the Tier 1 or Tier 2 supplier after cleaning and reconditioning. Alternatively, on a case-by-case basis, the container is sent to another supplier nearby, filled with their parts and sent to another OEM.
This solution is eco-friendly and sustainable and helps to reduce carbon footprints. Leadec is contributing to the reduction of tree felling by providing such solutions to the Indian industries.
For more information about the Green Factory Solutions go to: www.green-factory-solutions.com