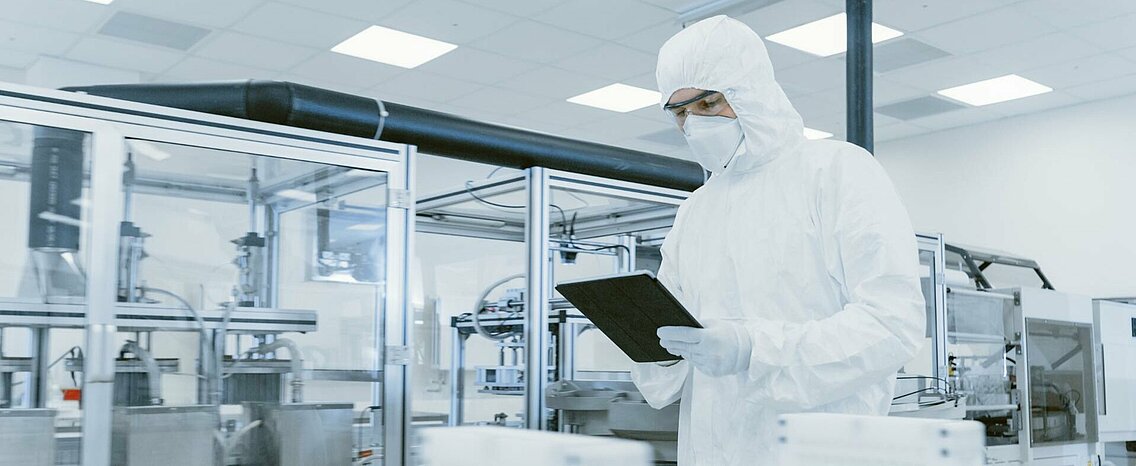
The high-tech world of chip manufacturing is all about precision in the nanometer range. Tiny particles such as dust, fibers and skin flakes on the components appear harmless at first but can have a massive impact on the sensitive structures of the semiconductor devices and lead to costly production downtime or defective chips. This is why these sensitive components require an appropriate environment in special cleanrooms: free of dust, electrostatic charge and moisture.
What does a cleanroom look like?
Cleanrooms are self-contained units, whether they are complete buildings, individual chambers or cleanroom tents within a larger space. Inside the cleanroom, appropriate cleanroom technology ensures compliance with the necessary environmental requirements: ventilation and air conditioning systems control compressed air conditions and keep room temperatures stable; cleanroom lights integrated into walls or ceilings ensure appropriate lighting conditions. “But it’s not just the furnishings that present a challenge for manufacturers; the cleaning and maintenance of a cleanroom and the associated technology are also of central importance,” says Dana Nikolaj, Business Director Semiconductor at Leadec, “and this is where Leadec comes into play.”
Sterile surfaces and low-particle air
In order to keep the cleanroom permanently clean, a customized cleaning concept is required. This also includes concentrating on only the absolutely necessary objects in the cleanroom when setting it up, installing seamless and crack-resistant cladding wherever possible and using abrasion-resistant materials. The combination of dry cleaning, for example with antistatic cloths, wet cleaning and disinfection, helps to reduce microbial contamination and ensure a virtually sterile environment.
Individual discipline and protective clothing
However, Dana Nikolaj also knows: “In addition to the systems, materials and machines in the cleanroom, people pose the greatest risk of contamination. That’s why strict hygiene regulations and the use of sterile cleanroom clothing apply. The Leadec teams are familiar with this special production environment and therefore work with lint-free cleanroom cloths. We minimize the risk of introducing particles with everything from mob caps, various covers and coveralls to hair and beard nets.”
Quality assurance with sensors
State-of-the-art sensor technology is used in cleanrooms to ensure seamless quality assurance of the working environment. The sensitive devices continuously monitor particle concentration, air flow, temperature and humidity.
Sustainable cleaning
Sustainability also plays an important role in cleanroom cleaning. Resource-saving cleaning processes, the use of biodegradable cleaning agents and the use of recycled materials help to reduce the environmental impact.
Expert knowledge for sensitive areas
“Cleanroom cleaning and working in semiconductor production is a complex and demanding field that requires in-depth specialist knowledge,” says Nikolaj, adding: “We at Leadec already have extensive experience of the special features that need to be taken into account when cleaning cleanrooms.” Leadec is operating in various production facilities of well-known manufacturers. In addition to cleanroom cleaning, the on-site teams also provide preparatory maintenance measures for the equipment and utility supply as well as logistics services within the fab. Through its Automation & Engineering Business Unit, Leadec offers automation solutions for networking individual utility supply systems (gas and chemicals) as well as other solutions within process automation and complete delivery and configuration of process control systems.