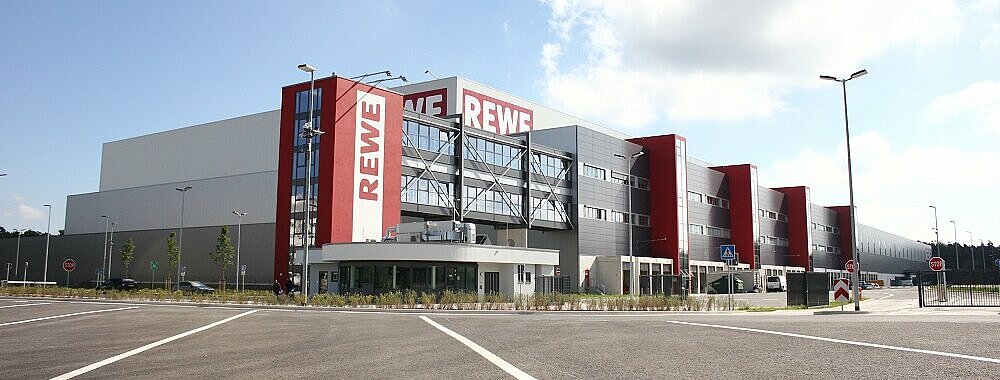
On 64,747 square meters, the REWE “RED 63” logistics hub, which opened in 2014, supplies around 5,000 supermarkets and partners with up to 600,000 packages daily. Maintenance of the facilities – from ventilation and heating to security zones – has been in Leadec’s hands since 2019. Leadec.os, our digital platform that seamlessly tracks and monitors every maintenance job, is part of the package. Leadec supervisor Milan Masek explains, “We have around 1,400 assets recorded in Leadec.os. Every single maintenance job is created digitally and assigned to one of our technicians. Once the work is done, there is immediate feedback into the system so that the progress of each job can be tracked.”
Transparency on a large scale
Given the size of RED 63, there’s a lot to do. Every month, the four-person Leadec team takes on an average of 40 to 50 scheduled maintenance jobs, ranging from testing electrical distribution panels to fire doors. Often, these consist of many individual steps.
“Using Leadec.os, we can track the status of all jobs. For this purpose, the platform displays all assets, provides information about maintenance requirements and potential malfunctions, and documents services provided in real time,” says Eckhard Futterlieb, responsible head of building services at the REWE distribution center. The platform not only improves plannability, but also offers paperless and audit-proof documentation. All maintenance logs and fault messages can be viewed directly.
In addition to scheduled maintenance activities, malfunctions or short-term requirements are also processed via Leadec.os. For such cases, notification is possible via the Leadec.os customer portal or via e-mail.
Using maps to get to the maintenance spot
In order to always quickly find the right system in the RED 36 hub of almost ten soccer fields, all geodata has been integrated into Leadec.os. This is because some of the 160 fire dampers or the 100 recirculating cooling units are well hidden in the building. “By means of longitude and latitude, the location of each asset is defined, and it can thus be quickly found by our service technicians and also by the technical REWE staff via Google Maps,” explains supervisor Milan Masek. “The more accurate the asset recording is, the easier it is.”
In the future, REWE plans to use Leadec.os even more intensively. “We process some of the notifications ourselves, which, however, have not been recorded digitally so far. In the future, we will have technician access to the platform and our teams will be able to liaise even more closely,” says Eckhard Futterlieb.